
PEAK
PERFORMANCE
Benchmarking Performance to Over 100 Mines.
Peak Performance
Peak Performance began in 1999, with the goal of providing:
-
Targeted Result-Based Training
-
Operational Efficiency (Supervisor Training)
-
Machine Upgrade Justification
-
Operating For Reliability
​​
We developed the AC-3 benchmarking software to separate these items into precise measurements. We have collected benchmarking data from 127 different mines from South America, North America, Africa, India and Australia.
​
We have benchmarking data on all makes and models of Electric Shovels, Hydraulic Shovels, Wheel Loaders, Track Hoes, Draglines as well as a variety of Haul Trucks and Support Equipment. From this we are continuing to develop best practices for mine equipment operations.
​
In 2024, we partnered with VISTA, to provide even better Training, Consulting and Benchmarking Services for our Customers. See real-world examples below.
Peak Performance and VISTA: Results You Can Measure
​​
View press release: Peak Performance and VISTA - Benchmarking from 127 mines enables targeted training (July. 2, 2024)​
​
Cycle Time Reduction Example:
The following example was taken at a mine on three different pieces of equipment. Using the AC- 3 benchmarking software, a baseline cycle time was established for each operator. A targeted training plan for each operator was developed (Benchmark 1).
​
After Implementation of the targeted training. Each operator was re-benchmarked (Benchmark 2) to quantify the results, and to determine if additional training was necessary.

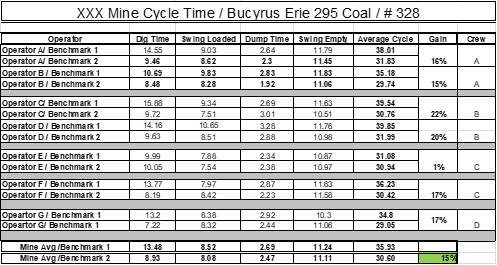
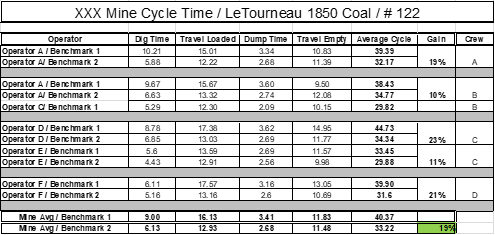
Utilization Example:
The following example was taken at a mine that was using a single 4100 Shovel. Using the AC- 3 benchmarking software, a baseline utilization was established for each crew. A combined mine profile was established to determine how much time was actually spent loading and how much time was spent on operational delays. A targeted training plan for the mine was developed (Benchmark 1).
​
After implementation of the targeted training each crew was re-benchmarked (Benchmark 2) to quantify the results. Additional training was provided to help increase utilization further (Benchmark 3). Additional goals were set where continuous improvement could be made.



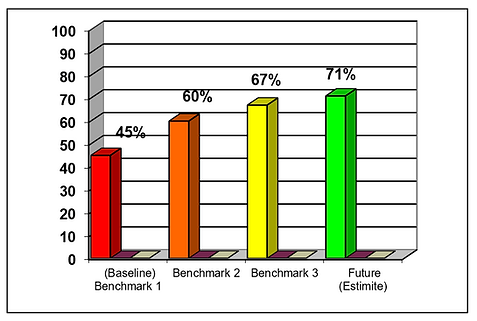
Productivity Checklist: (Supervisor Training)
The productivity checklist is a list of items that can enhance or reduce daily production. Our benchmark studies determined the occurrence and location of the following production delays.
-
85% of production losses occur on the shovel bench.
-
5% of production losses occur on the haul roads.
-
10% of production losses occur on the waste or ore dumps.
Delay management varies from operation to operation depending on location, personnel, union rules, state laws and equipment available to control these delays.
This check list was developed to help supervisors with safety checks as well as planning for productivity and delay management.​

Machine Upgrade:
The following example illustrates a mine that purchased a machine upgrade designed to increase the fill of the dipper. After about a month operating, they felt they were not getting the full value of this upgrade.
​
After benchmarking all the shovels, it was determined that the extra fill factor provided the most value when the truck was capable of hauling the extra material. To get the most out of the upgrade it would need to send trucks with the largest capacity to the upgraded shovel.

Maintenance Reduction:
A mine complained that their hoist rope life wasn’t what they thought it should be. After benchmarking, we found that the average operator accidently snapped the hoist ropes 10 times per shift. Further, we identified one operator who snapped the ropes167 times per shift. We targeted training to help that operator.
​
-
Hoist Rope Life
-
Mine Average / 10 Occurrences per Shift.
-
Individual Average / 167 Occurrences per Shift.

